Analysis of 5 Factors Affecting Air Spinning Quality
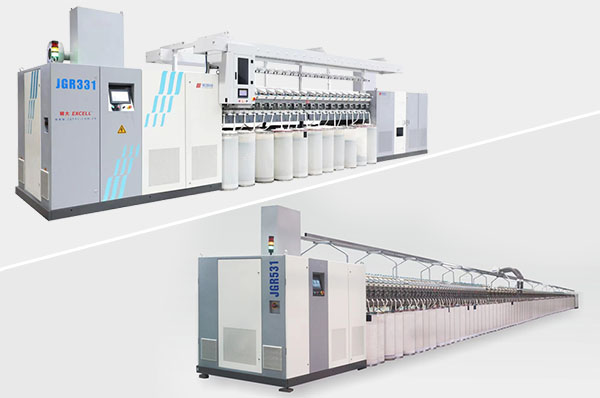
The following tasks are mainly completed in the air spinning process: opening and drafting the sliver to a single fiber state; removing impurities from the feed material; uniformly mixing the fibers; forming whiskers; agglomerating fibers; improving uniformity by combining degree; twisting; winding forming.
JGR331 Open End Spinning Machine (OE Spinning Machine) using suction type spinning box, bearing type rotary cup; The whole structure of the equipment adopts flat design to reduce the operation height. The applicable raw materials of the equipment are: pure cotton, pure polyester, polyester cotton, viscose and so on. It has the characteristics of energy saving and high efficiency.
JGR531 type rotor spinning machine borrowed JGR331 model design, using bearing rotary cup, the design of the spinning machine is aimed at the suitability of cotton, polyester, thread cotton, recycled cotton and their blends....
Theoretically speaking, during air spinning, a single fiber is condensed into a fiber ring in the condensing groove of the rotor, and then the fiber ring is pulled up in the opposite direction, but in fact, fiber bends will occur during this process due to other reasons. Hooks, fiber loops, fiber pieces and other deformations, etc., greatly affect the quality of air spinning. The quality of the yarn is affected by the quality of the fed sliver, mainly the length of the sliver fiber, the length uniformity, the fiber fineness and the impurity content. On the other hand, the better the separation state of the fibers during the conveying and agglomeration process, the better the yarn quality. The quality of sliver is controlled by the pre-spinning process. Carding is the key process of air spinning. It mainly removes impurities, carding and evenly mixes the fed raw materials. Therefore, adjusting the carding process parameters has a great impact on the quality of sliver. affect yarn quality. The following five main factors affecting the quality of air spinning are analyzed:
01 Carding:
Cylinder, cover and doffer play an important role in carding. When the cylinder arrives at the doffer with a layer of fiber, the end of the fiber hits the surface of the doffer and is grabbed by the doffer wire while the other end is still held by the cylinder wire. When the cylinder passes through the transfer zone, due to its high surface speed High, the fibers are pulled by the doffer wire and create tension. This cohesion makes the amount of fiber per unit area of the doffer 2 to 3 times that of the cylinder unit area. If the speed of the doffer increases, more pin teeth can participate in the carding. As the speed of the doffer increases, the agglomeration effect increases. Even if the ratio of the linear speed of the cylinder to the surface of the doffer decreases, the transfer effect of the fibers will also increase. If the speed of the doffer increases If it increases too much, the cohesion will decrease, and the transfer effect is closely related to the formation of fiber hooks. When other parameters remain unchanged, increasing the output by increasing the doffer speed will increase the needle surface load of the cylinder, which will increase the neps and reduce the evenness of the card sliver, so the yarn quality will deteriorate, that is, the U% value will become larger , the strength and appearance grade of the thread will be significantly reduced.
By adjusting the flat speed or flat flower content, it is possible to produce better quality slivers with laps of average mixed quality. When all other parameters remain the same, if only the flat speed is increased, the flat splinter will increase. At the same time, due to the enhanced carding effect, the impurities in the raw sliver will be reduced, and the short pile will also be reduced. The strength of the yarn can be improved, but the strong CV The % value will be reduced while the measured number of yarn defects and the U% value will not change, so the quality of the yarn and the appearance of the fabric will be improved.
02 Fiber length:
Fiber length does not play the same role as it does in ring spinning. The fiber length is related to the diameter of the rotor as follows:
Rotor diameter = fiber length * 1.2
The twist is transferred down to a specific point in the rotor condensor, called the stripping point, where there is a bundling area where the fibers are twisted. The length and stability of the clustering area are two parameters that determine whether the spinning process is stable, thus affecting the yarn breakage rate.
During the spinning process, the length of the bundled area fluctuates around an average value. Once the length of the bundled area is lower than the critical value and impurities hinder the transmission of twist, the end breakage will occur. The longer the fiber length, the higher the length uniformity , the spinning process is more stable.
03 Fiber fineness:
Fiber fineness is one of the main factors determining yarn breakage and spinning count. The optimal number of fibers in the yarn section (nf) can be calculated by the following formula: nf=15030/(yarn British count*mic)
This relationship shows that as the fiber becomes thicker, the yarn strength decreases. Coarse fiber spinning will also lead to deterioration of the yarn dryness CV%, and a higher twist coefficient should be used during spinning to ensure the strength of the yarn.
04 Fiber strength:
The strength of air spinning is linearly related to the strength of fibers. Most of the fibers in air spinning are in the state of hooks, and the degree of fiber shortening increases with the increase of fiber length. The following relationship can estimate the strong CSP of the yarn:
CSP=K(ls/f)0.35
Among them: K—constant; l—take 50% of the fiber length range (mm); s—take 1/8 of the fiber strength (g/tex); f——fiber fineness (mic).
05 Impurities:
Pre-spinning impurities are classified as follows: large impurities, fiber fragments, and dust. Large impurities can usually be effectively removed by the waste removal system of the air spinning machine. However, the kinetic energy of the dust due to the acceleration force prevents it from depositing between the teeth of the opening roller. The air buoyancy becomes flat, and some slightly larger dust will enter the rotor and be mixed in the fiber ring, resulting in an increase in the unevenness of the short segment of the yarn, resulting in a decrease in yarn strength and elongation at break.
Fiber fragments include broken seeds, sterile seeds, fibrous seed chips, soft seed skins, etc., which are not easy to remove during the entire processing process. They affect the transmission of twist in the rotor and greatly affect the appearance of the yarn. Even if they are removed by the opening rollers, they may still be deposited in the condensate chute and cause fly.
The degree of dust deposition increases with the increase of the impurity content in the fed sliver, and the higher the rotor speed, the smaller the diameter, the higher the deposition degree. Due to the uneven twist caused by dust deposition, the fabric produces "runners" and "cloud spots". The deposition of dust can also damage the evenness of the yarn and increase the hairiness of the yarn. Moreover, the deposition of dust will increase the number of yarn breaks during the spinning process. The causes and proportions of decapitation are as follows:
Produce cotton tuft: 31.5%;
Dust and flying flowers are deposited at the miscellaneous outlet and taken away by the rotor: 28.5%;
Impurities in cooked slivers that have not been removed in the cleaning and carding process: 24%;
Dust on the rotor: 16%.
Therefore, choosing a good feed material can reduce the impurity level and reduce the dust accumulation in the rotor.
06 Summary:
Based on the above analysis, proper selection of spinning raw materials and reasonable configuration of spinning process parameters, strengthening of raw material management and process management, especially reasonable adjustment of carding machine process settings, and measures to control, so that the yarn quality can be guaranteed.