Open End Machine, Rotor Spinning Machine Principle
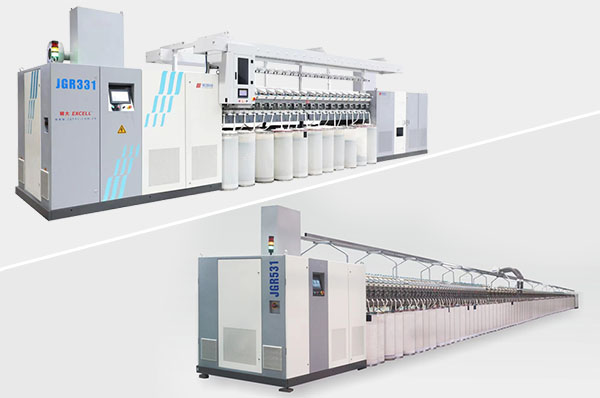
Rotor Spinning Machine Principle
The fed fiber slivers are opened into single fibers by the rotary carding roller covered with card clothing, transported to the inner wall of the high-speed rotating cup with the airflow, and form yarn tails in the condensation groove, and are drawn out by twisting into yarn at the same time. Wind into a bobbin. The main difference between rotor spinning and other open-end spinning methods is that the mechanism and function of coagulation and twisting are different. After the single fiber enters the rotor, it is first sent to the inclined surface of the inner wall of the rotor. Due to the high surface speed of the inner wall of the rotor, the fibers are arranged in parallel along the circumference of the inner wall. Under the action of centrifugal force, they slide into the coagulation groove at the largest diameter of the inner wall, where they are stacked into ring-shaped whiskers. This is the cohesion of fibers. process. During the coagulation process, the fibers are arranged circularly in the circumferential direction, so there is a merger effect. The rotor drives the AB yarn sections to rotate together at high speed, and at A, due to the friction of the twister, a twist is generated in the AB yarn section and the drawn yarn section. The twist in the yarn sliver in section AB is transmitted to the BC length of the yarn tail in the condensation groove due to the torsional moment, so that the yarn tail has a certain strength near the stripping point B, which can reduce broken ends. During normal spinning, the yarn tail is gradually stripped and drawn out from point B, so the rotation speed of the AB yarn segment generally exceeds the rotor speed, and the difference between the two linear speeds is the winding linear speed or output speed. The number of fibers at the stripping point B of the yarn tail in the condensation groove is equal to the number of fibers in the yarn section, and then gradually becomes thinner. Theoretically, the number of fibers at D at the end of the cycle should be zero, but in fact the fibers in the cup keep sliding down, so there are fibers at D point overlapping with the stripping point B. When the sliver is twisted and stripped out, the fibers located before point B along the rotating direction of the rotor become part of the sliver, while the fibers located behind point B are easily taken out and wound on the outer layer of the yarn body to form an air-flow yarn twisted fibers.
JGR331 Open End Spinning Machine (OE Spinning Machine) using suction type spinning box, bearing type rotary cup; The whole structure of the equipment adopts flat design to reduce the operation height. The applicable raw materials of the equipment are: pure cotton, pure polyester, polyester cotton, viscose and so on. It has the characteristics of energy saving and high efficiency.
JGR531 type rotor spinning machine borrowed JGR331 model design, using bearing rotary cup, the design of the spinning machine is aimed at the suitability of cotton, polyester, thread cotton, recycled cotton and their blends....