Yarn Processing/Making/Manufacturing
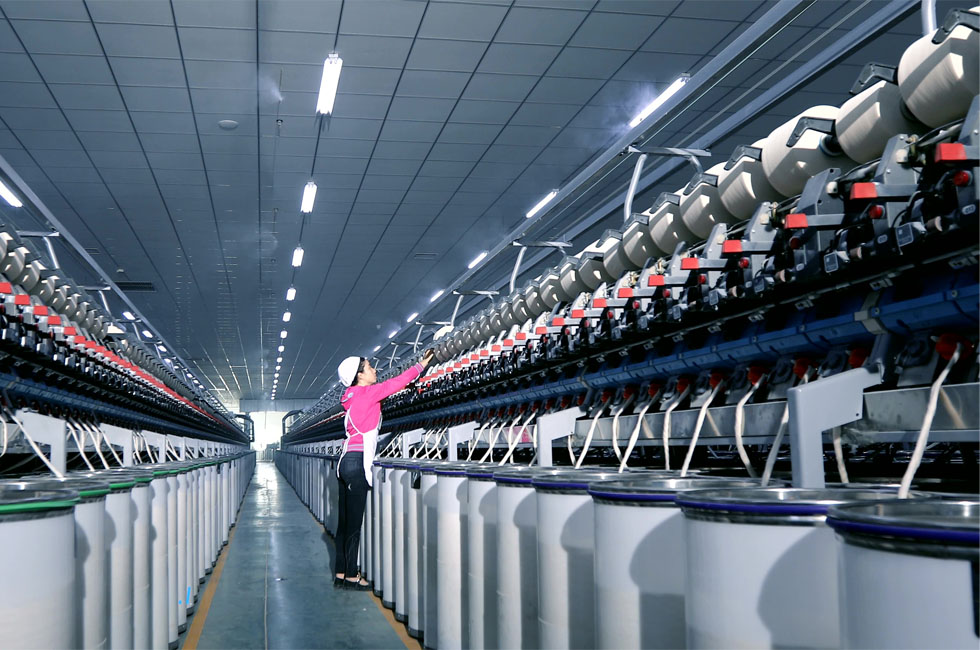
Yarn Processing/Making/Manufacturing Process
Yarn Processing/Making/Manufacturing process roughly includes:
1:Preparing the fibers 2:Carding 3:Combing 4:Drawing out 5:Twisting 6:Spinning
Urning synthetic fibers into yarn is not an easy process. It comprises a series of processes that decide the yarn characteristics like size, quality, texture, etc. Let’s walk you through the different steps of processing the fine quality yarns.
Yarn Processing/Making/Manufacturing Process
1: Preparing the fibers
Fibers are shipped in bales, which are opened by hand or machine. Natural fibers may require cleaning, whereas synthetic fibers only require separating. The picker loosens and separates the lumps of fiber and also cleans the fiber if necessary. Blending of different staple fibers may be required for certain applications. Blending may be done during formation of the lap, during carding, or during drawing out. Quantities of each fiber are measured carefully and their proportions are consistently maintained.
2: Carding
The carding machine is set with hundreds of fine wires that separate the fibers and pull them into somewhat parallel form. A thin web of fiber is formed, and as it moves along, it passes through a funnel-shaped device that produces a ropelike strand of parallel fibers. Blending can take place by joining laps of different fibers.
3: Combing
When a smoother, finer yarn is required, fibers are subjected to a further paralleling method. A comblike device arranges fibers into parallel form, with short fibers falling out of the strand.
4: Drawing out
JGT1000D Polyester DTY Yarn Draw Texturing Machine mainly used for POY yarn, through tensile and elastic energy in false twist deformation processed into a low false twist textured yarn (DTY polyester stretch yarn), processing in each ingot will read S and Z twist of double wire directly to step into a partnership with no residual torque silk, relative to the spindle joint stock after production, the machine production doubled.
After carding or combing, the fiber mass is referred to as the sliver. Several slivers are combined before this process. A series of rollers rotating at different rates of speed elongate the sliver into a single more uniform strand that is given a small amount of twist and fed into large cans. Carded slivers are drawn twice after carding. Combed slivers are drawn once before combing and twice more after combing.
5: Twisting
The sliver is fed through a machine called the roving frame, where the strands of fiber are further elongated and given additional twist. These strands are called the roving.
6: Spinning
The predominant commercial systems of yarn formation are ring spinning and open-end spinning. In ring spinning, the roving is fed from the spool through rollers. These rollers elongate the roving, which passes through the eyelet, moving down The sliver is fed through a machine called the roving frame, where the strands of fiber are further elongated and given additional twist. The predominant commercial systems of yarn formation are ring spinning and open-end spinning. Open-end spinning omits the roving step.
The sliver is fed through a machine called the roving frame, where the strands of fiber are further elongated and given additional twist. The predominant commercial systems of yarn formation are ring spinning and open-end spinning. Open-end spinning omits the roving step.
and through the traveler. The traveler moves freely around the stationary ring at 4,000 to 12,000 revolutions per minute. The spindle turns the bobbin at a constant speed. This turning of the bobbin and the movement of the traveler twists and winds the yarn in one operation.
Open-end spinning omits the roving step. Instead, a sliver of fibers is fed into the spinner by a stream of air. The sliver is delivered to a rotary beater that separates the fibers into a thin stream that is carried into the rotor by a current of air through a tube or duct and is deposited in a V-shaped groove along the sides of the rotor. As the rotor turns, twist is produced. A constant stream of new fibers enters the rotor, is distributed in the groove, and is removed at the end of the formed yarn.